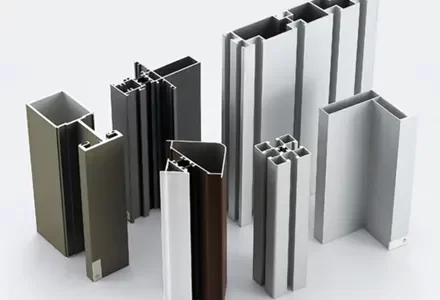
Aluminium Profiles
- Competitive OEM factory
- Factory area 60,000 square meters
- Owns 11 automatic extrusion equipment
- Specializing in the production of extruded aluminum profiles
Your trusted Aluminium Profiles manufacturer
Product type
Xingda has a wide range of extruded aluminum profiles, including aluminum door and window profiles, curtain wall profiles, industrial profiles, kitchen cabinet profiles, sunrooms, pergolas and fence profiles as well as some other architectural decorative aluminum profiles.
Advantage
Xingda is a company that specializes in designing and manufacturing different types of aluminum profiles for more than 30 years. Provide one-stop aluminum and accessories solutions as well as ODM and OEM services to more than 200 manufacturers and dealers around the world.
Surface treatment
Including anodizing, spraying, sandblasting, polishing, etc. to improve the surface performance, aesthetics and corrosion resistance of aluminum profiles.
Precision machining
such as CNC machining, turning, milling, etc., used for fine processing of aluminum profiles to meet high-precision requirements.
Xingda:Professional Aluminium Profiles manufacturer
Xingda works with you based on your specific needs and design requirements. We will provide customized aluminum profiles design solutions, including cross-sectional shape, size, etc.
Xingda will according to your application needs,We’ll introduce you to the different alloys and purities of aluminum profiles available and help you choose the most suitable material to meet your specific performance requirements.
Â
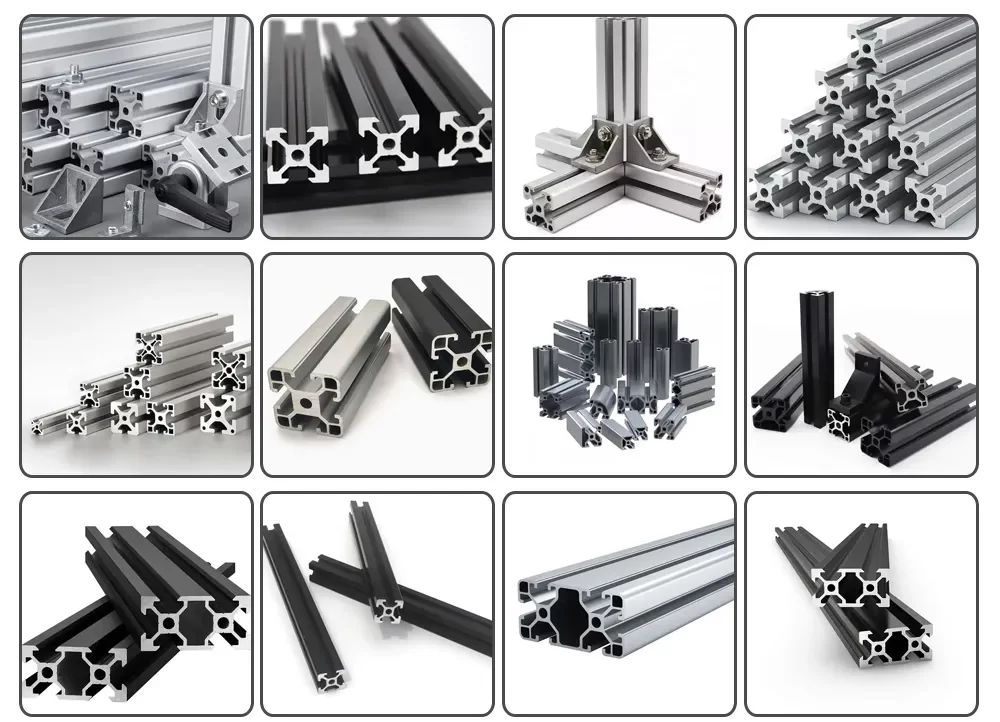
The quality control measures taken by Xingda during the aluminum profiles production process ensure that the aluminum profiles meet your technical requirements and standards, thereby providing high-quality aluminum profiles.
Let’s Support Your Bussiness and Reduce Cost For You
Xingda can custom your Aluminum Extrusions , Also can design your own Products, Even If idea ONLY.
Xingda: Your trusted extruded aluminum profile manufacturer
The high-quality aluminum profile factory is right in front of you. Xingda has an experienced in-house design and R&D team that handles aluminum profile forming, extrusion, surface treatment, CNC processing, etc.
From aluminum extrusion production to deep processing, everything is completed in Xingda’s own factory. With 31 years of aluminum profile manufacturing experience, we are positioned as a global aluminum profile solution provider based in China.
Xingda is a large-scale factory for extruded aluminum profiles, helping you develop and design differentiated products, allowing you to win more market share
Aluminum Profiles: The Ultimate Guide
When we talk about aluminum profiles, it refers to metal materials with specific cross-sections formed by extrusion and other processes using aluminum alloy as the base material. Its characteristics include light weight, high strength, good corrosion resistance and high plasticity, making it widely used in construction, automobiles, electronics and other fields. This sustainable material plays an integral role in modern manufacturing due to its wide range of uses and environmentally friendly properties.
- Are aluminum profiles non-ferrous metals?
- Is the aluminum profiles oxidized and rusted?
- Why do aluminum profiles need surface treatment?
- What are the key elements in aluminum profiles processing?
- Factors affecting the development trend of aluminum profiles?
- What should we pay attention to during the aluminum profiles extrusion process?
- What should you pay attention to when purchasing aluminum profiles?
- Optimal design of aluminum profile extrusion die?
- How thick is the anodized aluminum profiles?
- How thick is the powder coating of aluminum profiles?
- What should you pay attention to when anodizing aluminum profiles?
- What should you pay attention to when powder coating aluminum profiles?
- What properties should be considered when selecting aluminum profiles?
- How to avoid scratches on aluminum profiles?
- Why do aluminum profiles need surface treatment?
- Why do aluminum profiles need surface treatment?
Are aluminum profiles non-ferrous metals?
Aluminum profiles refer to products with various cross-sectional shapes made of aluminum and its alloys as basic materials through certain processes (such as extrusion, stretching, rolling, etc.), and are used in various fields of construction, transportation, etc. , industrial equipment, etc. Aluminum profiles themselves are not a metal, but aluminum products based on aluminum.
However, aluminum itself is a non-ferrous metal. Nonferrous metals refer to metals other than iron and steel, usually including copper, aluminum, magnesium, zinc, nickel, lead, etc. These metals share some common properties, such as being relatively light and having good electrical conductivity, making them suitable for a variety of specific applications.
Is the aluminum profiles oxidized and rusted?
The oxidation of aluminum profiles and the rust of iron are two different chemical processes.
Aluminum oxidation refers to the chemical reaction between aluminum and oxygen to form an oxide layer (usually aluminum oxide). Under normal circumstances, this oxide layer will protect the aluminum surface and prevent it from being further oxidized.
The rust of iron refers to the chemical reaction between iron and oxygen to form iron oxide, which usually appears as a reddish-brown rust layer, which will gradually corrode the surface of the iron.
Therefore, the oxidation of aluminum profiles and the rust of iron are two completely different phenomena. The oxide layer produced by the oxidation of aluminum profiles is usually a protective layer that helps protect the surface of the aluminum from corrosion. The rusting of iron is a corrosion process that gradually damages the surface of the iron.
It should be noted that under certain conditions, aluminum may also undergo some abnormal oxidation reactions, but in general, aluminum oxidation is a beneficial protective layer formation process, rather than iron-like rust.
Why do aluminum profiles need surface treatment?
Improve corrosion resistance: Surface treatment can form a protective oxide layer or coating, which effectively isolates external moisture, chemicals, etc., and improves the corrosion resistance of aluminum profiles.
Improve appearance: Surface treatment can make the surface of aluminum profiles present a more beautiful appearance. You can choose coatings or oxide layers of different colors, which improves the decorativeness of the product.
Improve hardness and wear resistance: Some surface treatment methods, such as hard anodizing, spraying, etc., can significantly improve the hardness and wear resistance of aluminum profiles, and are suitable for some occasions that require high wear resistance.
Improve thermal conductivity: Some surface treatment methods, such as conductive coating, thermal conductive coating, etc., can improve the thermal conductivity of aluminum profiles and are suitable for some occasions that require good thermal conductivity.
Improve weather resistance: Some surface treatment methods, such as painting, spraying, etc., can enhance the weather resistance of aluminum profiles, giving them a longer service life in harsh environments.
Improve surface roughness: Some surface treatment methods, such as sandblasting, polishing, etc., can adjust the surface roughness of aluminum profiles to meet the requirements of specific engineering projects.
Achieve specific functions: Some special surface treatment methods, such as anti-skid coating, electromagnetic shielding coating, etc., can give aluminum profiles specific functions.
In general, surface treatment can enable aluminum profiles to better exert their characteristics in different engineering projects and application scenarios, while also improving the appearance quality and service life of the product. Therefore, surface treatment is an important link that cannot be ignored in the processing and application of aluminum profiles.
What are the key elements in aluminum profiles processing?
Process selection: Different processing processes are suitable for different types of aluminum profiles, such as extrusion, stretching, rolling, etc. Choosing the right process is crucial to ensuring product quality and processing efficiency.
Equipment and Tools: Using the proper equipment and tools is crucial for efficient and precise machining of aluminum extrusions. This includes specialized equipment such as extruders, stretching machines, and rolling machines, as well as a variety of cutting, forming, drilling, and other tools.
Material preparation: Before processing aluminum profiles, it is necessary to ensure that the quality of the raw materials meets the requirements to avoid problems during the processing.
Process parameter control: During the processing process, some key process parameters need to be controlled, such as temperature, pressure, speed, etc., to ensure product quality and performance.
Safety measures: During processing, operators need to abide by corresponding safety regulations and wear necessary protective equipment to ensure personal safety.
Quality Inspection: After processing is completed, quality inspection is required to check whether the product meets the specified standards and requirements.
Surface treatment: If necessary, perform corresponding surface treatment, such as anodizing, spraying, etc., to improve the corrosion resistance and aesthetics of the aluminum profiles.
Environmental control: When processing aluminum profiles, the temperature, humidity and other factors of the working environment also need to be reasonably controlled to ensure the stability and quality of the processing process.
Personnel skills: Operators need to have corresponding skills and experience and be familiar with the operation methods of processing equipment to ensure the smooth progress of the processing process.
Process flow planning: The process flow needs to be reasonably arranged to ensure the connection and coordination between various links to improve production efficiency and product quality.
To sum up, the key elements of aluminum profiles processing cover many aspects such as process selection, equipment and tools, material preparation, process parameter control, safety measures, quality inspection, surface treatment, environmental control, personnel skills and process flow planning. The reasonable use and control of these factors will directly affect the quality and efficiency of aluminum profiles processing.
Factors affecting the development trend of aluminum profiles?
As an important industrial material, aluminum profiles will be affected by the following trends in future development:
Green environmental protection: As the global awareness of environmental protection increases, aluminum as a recyclable material will receive more attention. The production and use of aluminum profiles are relatively environmentally friendly and in line with the direction of sustainable development.
Lightweight technology: The lightweight and high-strength characteristics of aluminum profiles make it an important choice to replace traditional materials (such as steel), especially in the automotive, aerospace and other industries. With the continuous development of lightweight technology, aluminum profiles have broad application prospects.
High-performance alloys: The development and application of new aluminum alloys will further improve the performance of aluminum profiles, including strength, corrosion resistance, thermal conductivity, etc., to meet the high requirements for material performance in various industrial fields.
Intelligent manufacturing and automation: The production of aluminum profiles will increasingly rely on intelligent manufacturing and automation technology, improving production efficiency and reducing resource waste through advanced production equipment and intelligent control systems.
Customized production: With the increase in personalized demand, customized production will become an important development direction of the aluminum profiles industry. Manufacturers will offer more customized products tailored to specific customer needs.
Multi-field applications: Aluminum profiles will be used in more fields, such as construction, transportation, electronics, energy, etc. Especially in emerging industries, such as new energy vehicles, battery technology, etc., the demand for aluminum profiles will further grow.
International cooperation and technical exchanges: The aluminum profiles industry will be more open and international, strengthen cooperation and exchanges with other countries and regions, and jointly promote technological innovation and industrial development.
In general, the development trend of aluminum profiles will make significant progress in environmental protection, technological innovation, industrial upgrading and other aspects, providing more high-quality and sustainable material solutions for all walks of life.
Problems that need to be paid attention to during the extrusion process of aluminum profiles?
During the aluminum profiles extrusion process, you need to pay attention to the following important issues:
Material selection: Select the appropriate aluminum alloy material, considering its composition, hardness, strength and other characteristics to meet the requirements of the extrusion process.
Mold design: Design a suitable mold, including the feed end of the blank, the pressure head, the extrusion cavity and other parts, to ensure the accuracy and stability of molding.
Extrusion temperature: Control the appropriate extrusion temperature to ensure that the aluminum material can maintain sufficient plasticity during the extrusion process and avoid cracks or deformation.
Extrusion speed: Control the extrusion speed to avoid problems caused by too fast or too slow, and ensure the stability of the extrusion process and molding quality.
Lubrication: Use appropriate lubricants during the extrusion process to reduce friction, reduce extrusion force, and improve extrusion molding efficiency.
Extrusion ratio: Control the extrusion ratio well to avoid too large or too small extrusion ratio affecting the molding quality.
Cooling: After the extrusion is completed, the aluminum profiles is properly cooled to solidify its shape.
Quality inspection: During the extrusion process, timely quality inspection is carried out on the formed aluminum profiles, and any problems found can be adjusted and corrected in a timely manner.
Process parameter control: Control various process parameters during the extrusion process, including temperature, pressure, speed, etc., to ensure the stability and quality of extrusion molding.
Safety measures: During the extrusion process, operators need to comply with corresponding safety regulations and wear necessary protective equipment to ensure personal safety.
The above problems need to be reasonably controlled and dealt with during the extrusion process to ensure the molding quality and stability of aluminum profiles extrusion. In actual operation, it is best to have experienced professionals operate and control the extrusion process.
What should you pay attention to when purchasing aluminum profiles?
When purchasing aluminum profiles, you need to pay attention to the following important matters:
Clarity of purpose and demand: First, clarify the specific purpose for which you are purchasing aluminum profiles, such as construction, machinery manufacturing, aerospace, etc., to determine the required models, specifications and materials.
Material and alloy selection: Select the appropriate aluminum alloy material according to actual needs, taking into account its strength, corrosion resistance, thermal conductivity and other characteristics.
Specifications and dimensions: Select appropriate aluminum profiles specifications and dimensions based on project requirements to ensure they meet design requirements.
Quality certification and standards: Confirm whether the aluminum profiles supplier meets the corresponding quality certification standards, such as ISO certification, etc.
Appearance inspection: Carefully check the appearance of the aluminum profiles to ensure that the surface is smooth and free of obvious flaws, cracks, bubbles and other defects.
Weight check: For projects that require precise weighting, the weight of the aluminum profiles can be checked to ensure compliance.
Manufacturer’s reputation: To choose an aluminum profiles manufacturer with credibility and good reputation, you can learn about it by asking other customers for reviews or reference cases.
Performance testing: For aluminum profiles with special requirements, performance testing, such as strength testing, hardness testing, etc., can be performed to ensure that they meet the requirements.
price comparison:Compare the prices of different suppliers, pay attention to the comprehensive performance of quality and service, and choose products with high cost performance.
Delivery time requirements:Determine the delivery time requirements for aluminum profiles for your project and choose a supplier that can guarantee on-time delivery.
After-sales service:Understand the supplier’s after-sales service policy to ensure that you can receive timely technical support and solutions after purchase.
Contract details:Before purchasing, make sure to sign a clear contract, including product specifications, quantity, price, delivery date and other details to avoid subsequent disputes.
To sum up, when purchasing aluminum profiles, you need to fully consider the specific needs of the project and select appropriate materials, specifications and suppliers to ensure that the quality and performance of the aluminum profiles meet the expected requirements.
Optimal design of aluminum profiles extrusion die?
The optimized design of aluminum profiles extrusion dies is the key to improving production efficiency and product quality. Here are some suggestions for optimizing your design:
Material selection: Choose mold materials with good wear resistance and corrosion resistance, such as carbide, special alloy steel, etc., to extend the service life of the mold.
Mold structure design: A reasonably designed mold structure, including the feed end, extrusion cavity, discharge end and other parts, ensures the molding quality and accuracy of aluminum profiles.
Surface treatment: Surface treatment of the mold surface, such as hard chromium plating, grinding and polishing, etc., to improve the wear resistance of the mold and reduce surface defects of aluminum profiles.
Temperature control: Design a suitable mold cooling system to keep the mold within a suitable temperature range to ensure the stability of the extrusion process.
Reduce dead corners and welds: Minimize dead corners and welds in the mold to avoid uneven stress distribution during the extrusion process and reduce the forming quality of aluminum profiles.
Strengthen support and stiffness: Add appropriate support structures to the mold design to enhance the overall stiffness of the mold and avoid deformation or vibration during the extrusion process.
Mold wear monitoring: Regularly inspect and monitor the mold for wear, detect wear in a timely manner and repair or replace it to ensure long-term stable use of the mold.
Mold maintenance and upkeep: Establish a regular maintenance and upkeep system for the mold, including cleaning, lubrication, inspection, etc., to extend the service life of the mold.
Mold parameter adjustment: Flexibly adjust the mold process parameters, such as temperature, pressure, speed, etc., according to actual production conditions to ensure the stability and quality of extrusion molding.
Mold design optimization software application: Use professional mold design software to conduct simulation analysis and optimized design to help improve the performance and molding quality of the mold.
By comprehensively considering the above factors, the design of the aluminum profiles extrusion die can be effectively optimized to improve production efficiency and product quality. At the same time, customized design and adjustment are required based on specific extrusion processes and product requirements.
How thick is the anodized aluminum profiles?
Anodizing is a method commonly used for surface treatment of aluminum profiles. It forms a dense and uniform oxide layer through electrochemical reaction in a specific electrolyte. The thickness of this oxide layer can be controlled according to specific process conditions and requirements, usually between 5 microns and 25 microns, and different processes and requirements may vary.
Specifically, the thickness of anodized aluminum profiles can be divided into the following common grades:
Conventional oxide layer: The thickness of the conventional anodized layer is generally between 5 microns and 10 microns, which is suitable for general decorative and protective requirements.
Medium oxide layer: The thickness of the medium anodized layer is between 10 microns and 15 microns. It has good corrosion resistance and wear resistance and is suitable for some occasions with slightly higher performance requirements.
Hard oxide layer: The thickness of the hard anodized layer is generally between 15 microns and 25 microns. It has high hardness and wear resistance and is suitable for some occasions that require high surface hardness.
The appropriate oxide layer thickness needs to be selected based on specific application requirements and engineering projects to ensure that the aluminum profiles has good performance and durability in actual use. At the same time, when performing anodizing treatment, process parameters need to be strictly controlled to ensure that the thickness of the oxide layer meets the requirements.
How thick is the powder coating of aluminum profiles?
The thickness of aluminum profiles powder coating can be adjusted according to actual needs and specific application scenarios. Typically, the thickness of a powder coating is controlled within a specific range to ensure the performance and appearance of the coating.
The following are typical powder coating thickness ranges:
General powder coating: Under normal circumstances, the thickness of conventional powder coating is between 60 microns and 120 microns, which can provide better surface protection and decorative effects.
Thick coating: For some special requirements, if additional corrosion resistance or wear resistance is required, thick coating can be selected, with a thickness of 150 microns to 250 microns.
Thin coating: In some applications that have strict requirements on coating thickness, thin coating can be selected, and its thickness can be between 40 microns and 60 microns.
It should be noted that the specific powder coating thickness will also be affected by factors such as the coating process, coating equipment, and coating characteristics. Therefore, when performing powder coating treatment, it is best to determine the appropriate coating thickness range based on specific project needs, combined with the actual situation and the coating manufacturer’s recommendations.
What should you pay attention to when anodizing aluminum profiles?
When anodizing aluminum profiles, you need to pay attention to the following matters to ensure the effect and quality of the treatment:
Material and alloy selection: Choose the appropriate aluminum alloy material. Different alloys will affect the oxidation process and results.
Cleaning and decontamination: Before oxidation, aluminum profiles need to be thoroughly cleaned and decontaminated to ensure a clean surface.
Set appropriate process parameters: including current density, temperature, electrolyte composition, etc. Set appropriate process parameters according to specific conditions.
Mold design: If a mold is involved, ensure that the mold surface is smooth and has no obvious flaws to avoid affecting the uniformity of the oxide layer.
Avoid bubbles and hydrogen gas precipitation: Control the stirring and ventilation of the electrolyte during the oxidation process to avoid bubbles staying on the aluminum surface and producing an uneven oxide layer.
Control the oxidation time: According to the required thickness and properties of the oxide layer, control the oxidation time to avoid excessive or insufficient.
Quality inspection: Conduct quality inspection on the oxidized aluminum profiles, including oxide layer thickness, hardness and other indicators to ensure compliance with requirements.
Post-processing: After oxidation is completed, subsequent processes such as cleaning and sealing may be required to protect the oxide layer.
Environmental protection requirements: It is necessary to comply with relevant environmental protection regulations and standards to treat waste water and waste liquid.
Safety measures: The oxidation process involves electrolyte and electric current, which needs to ensure the safety of operators and avoid accidents.
These matters require special attention when anodizing aluminum profiles to ensure that the quality and performance of the oxide layer meet the expected requirements. At the same time, before performing oxidation treatment, it is best to consult a professional materials engineer or experts in related fields to ensure that the most appropriate process parameters and methods are selected.Â
What should you pay attention to when powder coating aluminum profiles?
When powder coating aluminum profiles, you need to pay attention to the following matters to ensure the effect and quality of the treatment:
Preparation work: Before spraying, make sure the surface of the aluminum profiles is clean and flat, and remove surface oil, dust and oxide layers.
Surface treatment: If necessary, pre-treatment such as sanding and pickling can be carried out to improve spray adhesion and coating quality.
Spraying environment: Choose a suitable spraying environment to avoid external factors such as wind or dust from affecting the spraying effect.
Painting equipment: Ensure that spray guns, equipment and other painting equipment are in good condition to ensure the stability of the spraying process.
Powder coating selection: Choose the appropriate powder coating according to actual needs, including color, type and quality.
Spraying technology: Control the spraying distance, spraying speed and angle to ensure that the paint adheres evenly to the aluminum surface.
Coating thickness control: Control the coating thickness according to project requirements. It usually needs to be adjusted within the thickness range.
Curing and baking: Send the coated aluminum profile into the oven for curing and baking to ensure that the coating is cured and adheres firmly.
Quality inspection: Conduct quality inspection on the sprayed aluminum profiles, including the flatness, adhesion and other indicators of the coating.
Environmental requirements: Comply with environmental regulations and standards for paint spraying, and handle waste paint and waste water.
Safety measures: When chemicals and high temperatures are involved, operator safety needs to be ensured and accidents avoided.
The above matters need special attention when powder coating aluminum profiles to ensure that the spraying effect and quality meet the expected requirements. At the same time, it is best to consult a professional coating engineer or an expert in the relevant field before spraying to ensure that the most appropriate spraying method and coating type are selected.
What properties should be considered when selecting aluminum profiles?
When selecting an aluminum profiles, there are a variety of performance indicators that need to be considered to ensure it is suitable for a specific application. The following are some common aluminum profiles performance indicators:
Mechanical properties: including tensile strength, yield strength, elongation, etc. These performance indicators determine the load-bearing capacity and deformation performance of aluminum profiles when stressed.
Hardness: The hardness of aluminum profiles can be evaluated through different hardness testing methods (such as Brinell hardness, Rockwell hardness, etc.). The higher the hardness, the better the scratch and wear resistance of the material.
Corrosion resistance: The corrosion resistance of aluminum profiles refers to its ability to resist corrosive media such as chemicals, moisture, salt spray, etc.
Electrical conductivity and thermal conductivity: Aluminum is an excellent electrical and thermal conductive material. These two properties are very important for applications that require conductive current or heat transfer.
Processability: Including processing properties such as extrusion, drawing, stamping, and welding, which determine the plasticity and formability of aluminum profiles during the manufacturing process.
Density: The density of aluminum is relatively low, which gives aluminum profiles an advantage in some applications where lightweighting is required.
Thermal expansion coefficient: This index affects the dimensional changes of aluminum profiles under temperature changes, and is of great significance for applications in high or low temperature environments.
Surface treatment performance: including the applicability of surface treatments such as painting, anodizing, and spraying, which affects the aesthetics and weather resistance of aluminum profiles.
Environmental protection: Considering environmental protection requirements, it is necessary to choose aluminum profiles that meet relevant standards to avoid adverse effects on the environment.
Cost: The cost of aluminum profiles is also an important consideration, and it is necessary to seek economical and practical options while meeting performance requirements.
In practical applications, different performance indicators will be focused on according to specific engineering projects or product requirements. Therefore, when selecting aluminum profiles, various properties need to be comprehensively considered to meet the requirements of specific scenarios.Â
How to avoid scratches on aluminum profiles?
To avoid scratches on aluminum profiles, you can take the following measures:
Proper storage and transportation: During storage and transportation, avoid contact with hard objects, especially direct contact with sharp objects to avoid scratching the surface.
Use protective measures: During handling, transportation, and installation, use appropriate protective measures, such as cloth, foam pads, etc., to isolate aluminum profiles from other objects.
Avoid contact with surfaces with hard particles: Avoid direct contact between aluminum profiles and floors, countertops and other surfaces that may have hard particles, especially when moving or installing.
Choose appropriate packaging: During the transportation and storage stages, use appropriate packaging materials and methods to ensure that the surface of the aluminum profiles is protected from friction and scratches.
Avoid direct contact of tools and equipment: During processing and installation, use appropriate tools and equipment to avoid direct contact of their hard surfaces with the surface of the aluminum profiles.
Regular inspection and cleaning: Regularly inspect the surface of aluminum profiles to remove dust, dirt and other impurities on the surface to avoid scratches during friction.
Follow correct installation and use methods: During the installation and use of aluminum profiles, follow correct operating procedures to ensure that unnecessary scratches are avoided.
Avoid contact with sharp objects: Avoid using sharp objects to directly contact the surface of the aluminum profiles, such as sharp blades, sharp metal tools, etc.
Coating protection: Aluminum profiles can be treated with corresponding surface treatments, such as spraying, anodizing, etc., to form a protective layer to reduce the occurrence of scratches.
Conduct training and education: Train and educate practitioners on how to avoid scratches on aluminum profiles during operations.
By taking these measures, you can effectively avoid scratches on aluminum profiles during storage, transportation, processing and installation, and protect their surface quality and aesthetics. “
Why do aluminum profiles need surface treatment?
The main purposes of surface treatment of aluminum profiles include the following aspects:
Improve corrosion resistance: Surface treatment can form a protective oxide layer or coating, which effectively isolates external moisture, chemicals, etc., and improves the corrosion resistance of aluminum profiles.
Improve appearance: Surface treatment can make the surface of aluminum profiles present a more beautiful appearance. You can choose coatings or oxide layers of different colors, which improves the decorativeness of the product.
Improve hardness and wear resistance: Some surface treatment methods, such as hard anodizing, spraying, etc., can significantly improve the hardness and wear resistance of aluminum profiles, and are suitable for some occasions that require high wear resistance.
Improve thermal conductivity: Some surface treatment methods, such as conductive coating, thermal conductive coating, etc., can improve the thermal conductivity of aluminum profiles and are suitable for some occasions that require good thermal conductivity.
Improve weather resistance: Some surface treatment methods, such as painting, spraying, etc., can enhance the weather resistance of aluminum profiles, giving them a longer service life in harsh environments.
Improve surface roughness: Some surface treatment methods, such as sandblasting, polishing, etc., can adjust the surface roughness of aluminum profiles to meet the requirements of specific engineering projects.
Achieve specific functions: Some special surface treatment methods, such as anti-skid coating, electromagnetic shielding coating, etc., can give aluminum profiles specific functions.
In general, surface treatment can enable aluminum profiles to better exert their characteristics in different engineering projects and application scenarios, while also improving the appearance quality and service life of the product. Therefore, surface treatment is an important link that cannot be ignored in the processing and application of aluminum profiles.