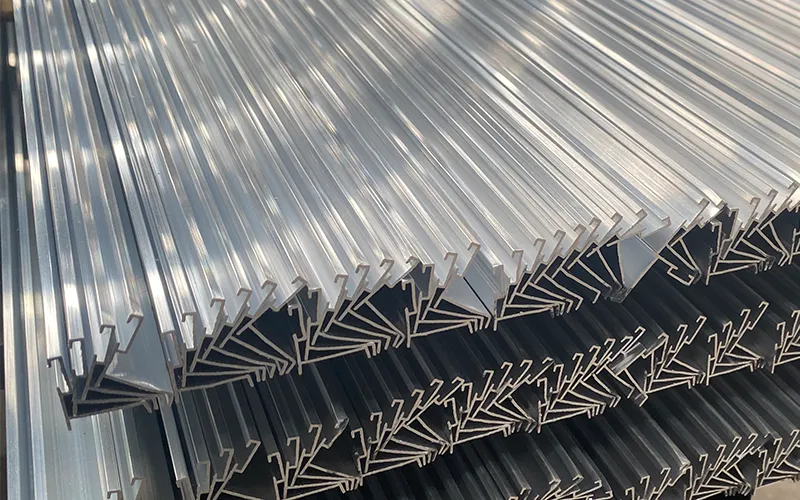
Anodized aluminum profiles
- Imported lots of highly advanced
- Factory direct delivery
- Obtain the honor of national
- production equitment from abroad
Your trusted anodized extruded aluminum profile manufacturer
Anodizing is achieved by placing an aluminum piece as an anode in an electrolyte and passing direct current through it. During the electrolysis process, a dense and hard oxide film will form on the aluminum surface. This film is aluminum oxide.
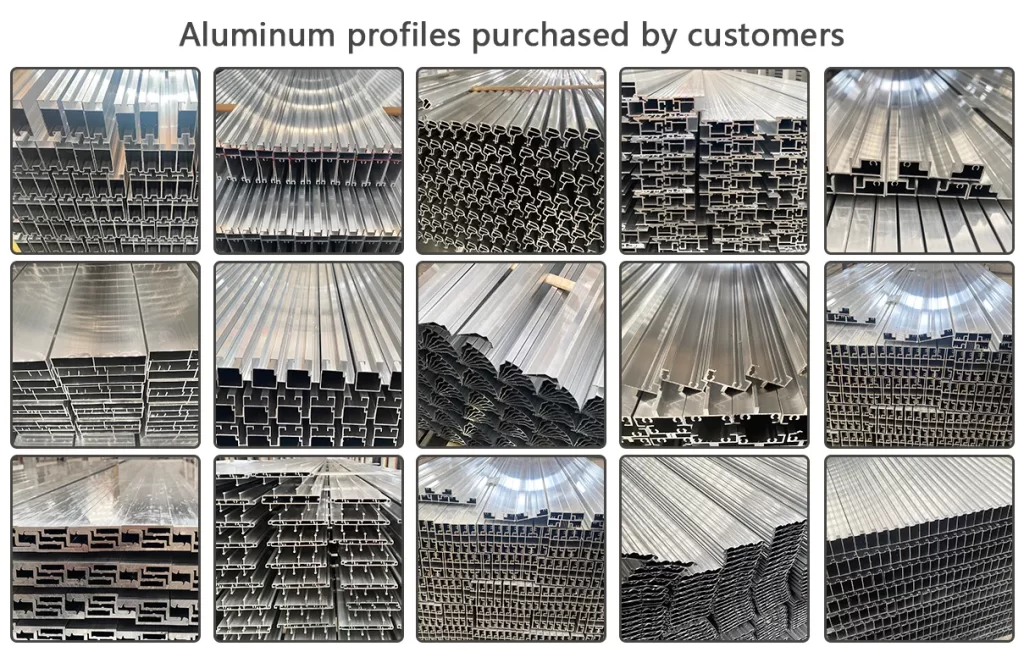
Xingda’s technical team has extensive experience in anodized extruded aluminum profiles. They have deep professional knowledge in electrochemical treatment, process flow, equipment operation, etc., which can ensure the stability and efficiency of the production process.
Xingda can customize anodized extruded aluminum profiles of different specifications and shapes according to your needs to meet the needs of your specific applications.
The surface of anodized extruded aluminum profiles usually presents a uniform and decorative appearance. Xingda can color it according to your needs or retain the original metallic color.
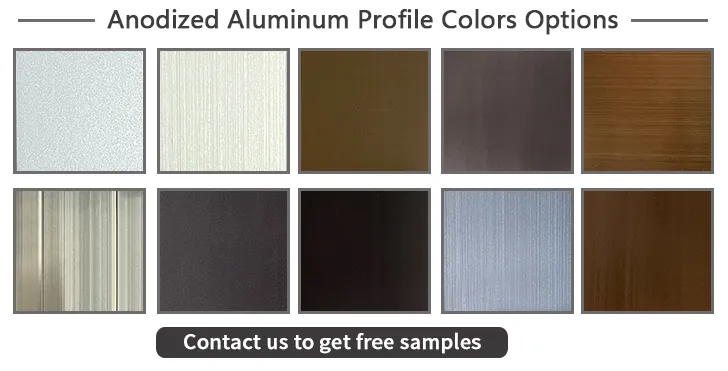
Anodizing extruded aluminum profile process flow
Anodizing extruded aluminum profiles is a complex process that involves multiple stages of processing to ensure a uniform and dense oxide film is formed on the surface of the extruded aluminum profiles. The following is the detailed process flow of anodized extruded aluminum profiles:
1. Preprocessing stage:
Before starting anodization, the extruded aluminum profile first needs to be pre-treated to ensure that the surface is clean and free of any impurities.
Remove oil:There is usually some grease, dirt, etc. attached to the surface of extruded aluminum profiles. In the degreasing stage, alkaline detergents or solvents are usually used to clean the aluminum profile surface to ensure that all grease is removed.
Cleaning:Cleaning is a critical step in ensuring a clean surface. Alkaline cleaners or other cleaning solutions are usually used to completely remove grease, dust and impurities from the surface.
2. Pickling stage:
Pickling is to remove scale and other possible impurities on the surface of extruded aluminum profiles.
Pickling tank:The extruded aluminum profile is placed in an acidic electrolyte. The solution in this electrolytic tank is usually an acidic medium containing sulfuric acid or phosphoric acid.
Pickling process:In the electrolytic cell, the surface of the extruded aluminum profile will be corroded by the acidic medium to remove scale and impurities. The pickling time and acid concentration need to be controlled according to specific conditions.
3. Anodizing stage:
The pickled extruded aluminum profiles are placed in an electrolytic bath containing a specific electrolyte and become the anode.
Electrolyte:The electrolyte is usually composed of sulfuric acid, aluminum sulfate, oxalic acid, etc. The specific composition and concentration will be determined based on the required oxide film thickness and other process parameters.
Current density control:During the anodizing process, the thickness of the oxide film can be adjusted by controlling the current density. The higher the current density, the thicker the thickness of the oxide film.
Electrolyzer temperature control:The temperature of the electrolyte is also an important factor affecting the thickness of the oxide film, and is usually controlled within a certain temperature range.
Electrolysis time:The time for anodizing depends on the required oxide film thickness and other process parameters, and usually ranges from several minutes to tens of minutes.
4. Closed stage:
After anodizing, tiny pores may exist in the oxide film. In order to improve the sealing and corrosion resistance of the oxide film, sealing treatment is usually performed.
Sealing agent:Soak the extruded aluminum profile in a sealant, which will fill the micropores in the oxide film and improve its sealing.
5. Wash and dry:
After the sealing stage is completed, the treated extruded aluminum profiles need to be cleaned to remove residual electrolyte and sealing agent. The aluminum profile is then dried to ensure its surface is dry.
The above is the detailed process flow of anodized extruded aluminum profiles. Each stage is crucial, and together they ensure the final formation of a uniform and dense oxide film, improving the performance and application value of extruded aluminum profiles.