Aluminum square tubing suppliers near me
- Complete specifications, sufficient stock, fast delivery
- Professional customized aluminum tube profiles
- All-round after-sales service
- You can get more profit
Aluminium tube suppliers
Xingda provides high-quality molds, castings, stamping parts, CNC machining and mold making, can give you the best price, best quality
• 31 years of aluminum tube extrusion experience
• Samples are provided free of charge
• Cost is cheaper than CNC factory
• Provide one-stop service
Xingda:You need extruded aluminum tube manufacturers and suppliers
Since its establishment in 1992, Xingda factory has been producing high-quality extruded aluminum tubes. We have 31 years of experience in aluminum tube production
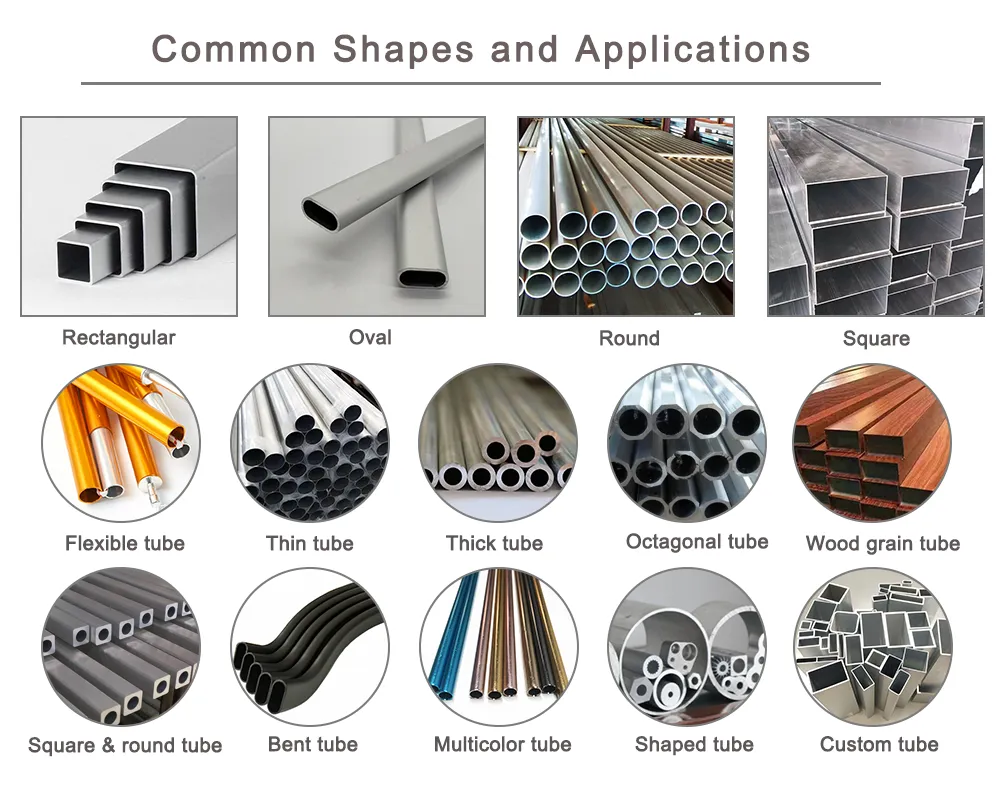
Product name | Aluminum Tube |
Surface Treatment | Mill Finish/Powder Coating/Anodizing/Wooden Grain/Electrophoresis |
Characteristics | strong,stylish,durable,corrosion-resistant. |
Size Customized | same as drawings or samples |
Alloy | 6063 T5/T6 |
Surface colors | Ref powder coating color sheet and customized color available |
Usage | aluminum profile for windows/ doors/ decoration/ construction/ curtain wall |
Packing | Protective film +plastic film or EPE +kraft paper |
Moulding | 1. There is no charge for using our molds;2. Use customer drawings, open molds, and free mold fees after reaching the quantity; |
Shape | Round, Round , Square, Triangle ,Rectangular |
Al (Min) | 98.8% |
Our advantages | OEM&ODM service |
Experience | 31years aluminum extrusion experience |
Quality | Guarantee Surface color can be stable for 10~20 years indoor using. |
Feature | Easy to stretch,has good formability, weldability, machinability |
Xingda’s extruded aluminum tubes range in size from 10mm to 154.4mm,with different wall thicknesses for you to choose from
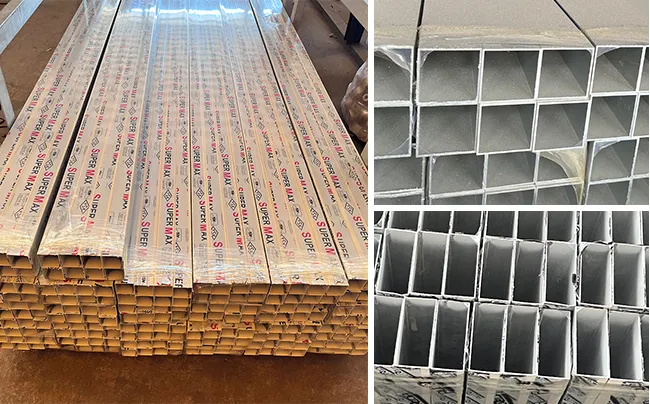
Xingda has more than 20,000 aluminum profile molds,if our existing extruded aluminum tubes are not suitable for you,we can make exclusive molds according to your design
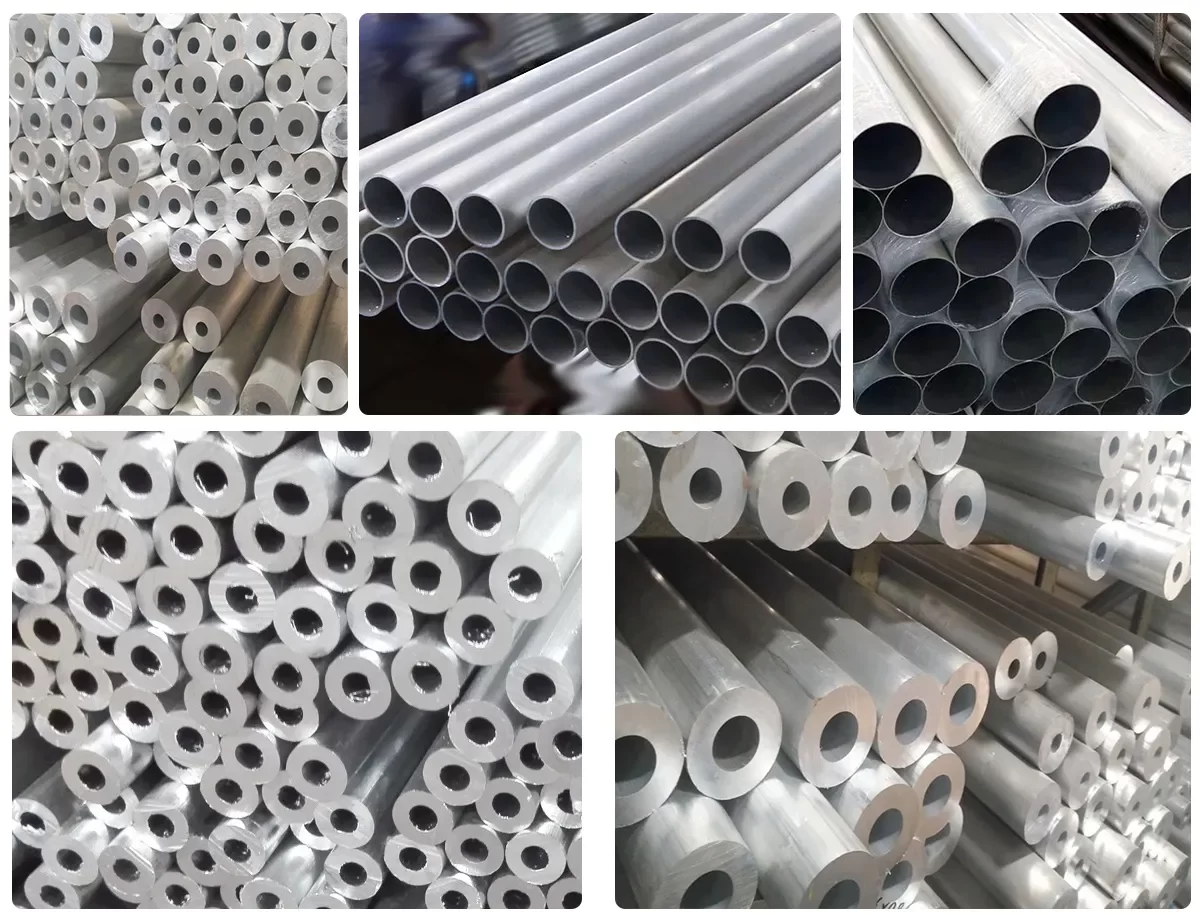
The material of extruded aluminum tubes that buyers often purchase is 6063 T5, and extruded aluminum tubes made of 6061 T5 and T6 are also more popular.
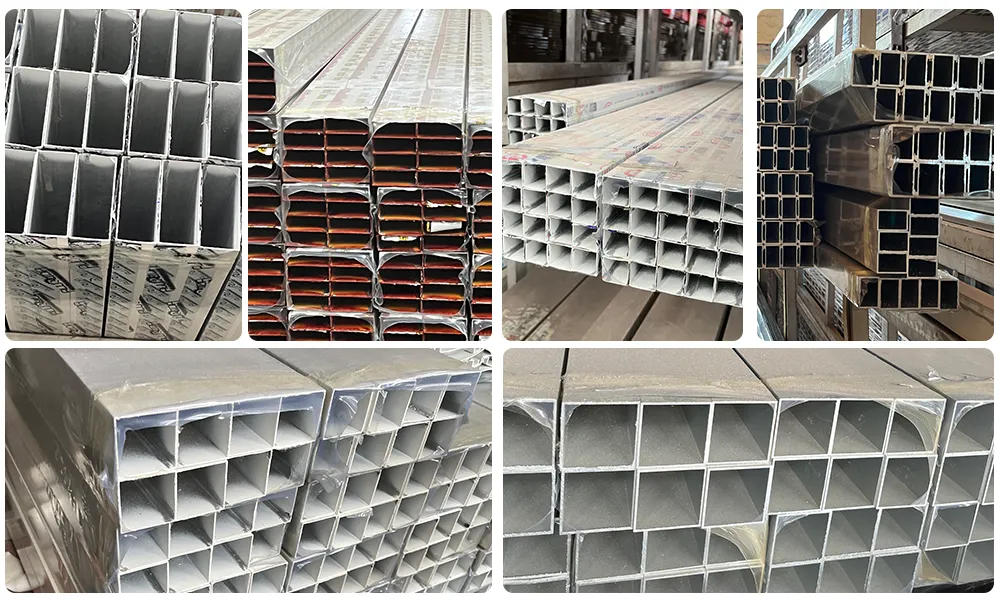
Xingda can provide the extruded aluminum tubes you need,and the surface can be anodized, sandblasted and oxidized, sprayed
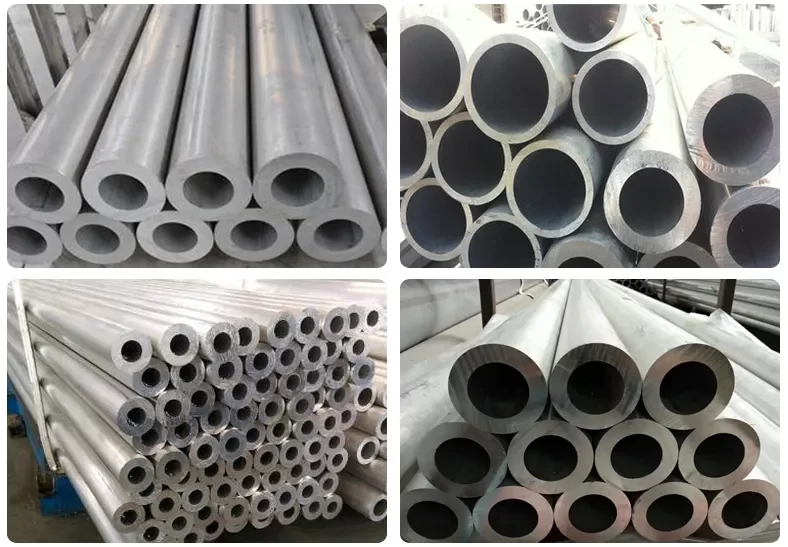
Extruded aluminum tubes are made of different materials and have different strengths, and the price will also be different.Xingda has stock in stock, welcome to consult
Frequently asked questions and answers about extruded aluminum tubes
Usually it takes about 15 days to produce new molds and samples, we will try our best to provide you according to your needed time.
We need to receive your drawings to calculate the price of extruded aluminum tubes
Our extruded aluminum tubes are manufactured in strict compliance with national and international standards and we test each product
Before delivery. If you would like to see our quality certifications and various test reports, please ask us.
The choice is because of quality and then price, we can give you both. In addition, we can also provide professional products
Inquiry, smooth delivery, excellent customer solution advice.
We accept multiple file formats such as DXF, DWG and IGES.
Yes! We are an aluminum profile factory with 31 years of experience in producing extruded aluminum tubes.
Our extrusion factory is located in Foshan City, Guangdong Province, China.
Products you may be looking for
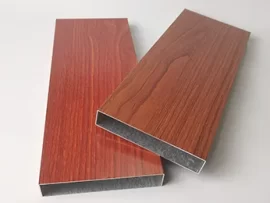
aluminum square tubing

aluminum rectangular tubing
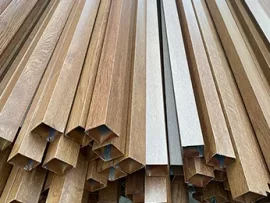
thin wall aluminum tubing
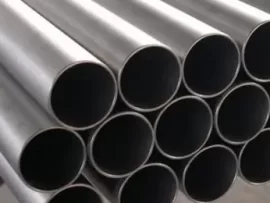
aluminium round tube
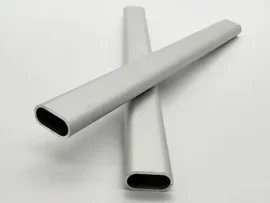
oval aluminum tubing
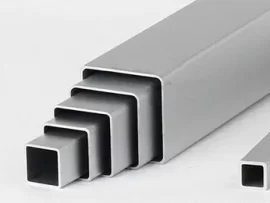
hollow aluminum tube
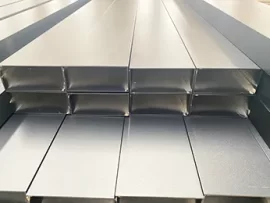
large aluminum tubing
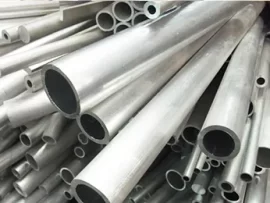
thick wall aluminum tubing
Xingda:Trusted China Aluminum Extruded Tube Manufacturer and Supplier
Xingda can provide you with thin-wall and thick-wall extruded aluminum tubes, these two types of aluminum tubes may be different in terms of usage, characteristics and manufacturing process, etc.
Thin-walled aluminum tubing is characterized by a relatively thin wall thickness and is typically used in applications where weight and volume are critical.
They are widely used in aerospace, automobile manufacturing, bicycle manufacturing, furniture manufacturing and other fields.Due to its light weight, high strength and good corrosion resistance, thin-walled aluminum tubes are especially suitable for scenarios requiring lightweight design.
Heavy-walled aluminum tubing has a larger wall thickness and is typically used in applications requiring greater strength and pressure resistance.
These extruded aluminum tubes are used in industrial equipment, building structures, conveying liquids or gases, etc.
Due to its higher pressure resistance, thick-walled aluminum tubes are often selected to withstand greater mechanical or pressure loads.
Whether it is a thin-walled tube or a thick-walled tube, the manufacture of extruded aluminum tubes usually involves processes such as extrusion,rolling, welding, etc.
Xingda: Extruded Aluminum Tube Buying Guide
As a multi-functional material, extruded aluminum tube can give full play to the advantages of extruded aluminum tube by correctly selecting the appropriate extruded aluminum tube material and specifications.
Before you buy, you need to know what size extruded aluminum tube is suitable for your project, and confirm whether the extruded aluminum tube provided by the supplier has passed some international or industry certifications, which can ensure that it is of good quality and meets the standards.
If your project is unique, it may require extruded aluminum tubing of special dimensions or characteristics. You can consult the supplier if it can be customized according to your needs.
Before officially buying, it is best to find a supplier to get a sample of the aluminum tube. This way you can better understand whether the product meets your requirements.
In this guide, let you learn about extruded aluminum tubing to determine the type and size of extruded aluminum tubing you need
- What is extruded aluminum tube
- Properties of Extruded Aluminum Tubes
- What types of extruded aluminum tubes are there?
- Different series of extruded aluminum tubes
- Production process of extruded aluminum tube
- Manufacturing process of aluminum tube
- Links Between Extruded Aluminum Tubes
- Quality testing of extruded aluminum tubes
- Specifications and standards for extruded aluminum tubes
- Straightening method of extruded aluminum tube
- Anti-corrosion and anti-rust treatment of extruded aluminum tube
- Application of extruded aluminum tube
What is Extruded Aluminum Tube?
The extruded aluminum tube is a hollow tubular structure made of aluminum alloy as the main material. It can have one or more closed through holes, and the wall thickness and cross-section are uniform.
Properties of Extruded Aluminum Tubes?
Lightweight: The lightweight nature of extruded aluminum tubing is one of its most attractive features. Extruded aluminum tubing is a lightweight metal with a relatively low density, which allows extruded aluminum tubing to significantly reduce overall weight when building structures and manufacturing products. This is very useful in fields such as construction and car manufacturing, where energy consumption can be reduced and efficiency can be improved.
Good thermal conductivity: The thermal conductivity of extruded aluminum tubes is also worthy of attention. Extruded aluminum tubes have excellent thermal conductivity, making them excellent in heat dissipation and thermal management. In electronic equipment, automotive engines, and other applications that require efficient heat transfer, extruded aluminum tubing plays an integral role as a heat sink to help keep equipment running properly.
Corrosion Resistance: The corrosion resistance of extruded aluminum tubing is another key factor for its wide application. Since a natural oxide layer is formed on the surface of the extruded aluminum tube, it has good resistance to oxidation and corrosion in the environment. This allows the extruded aluminum tubing to maintain its appearance and performance for both indoor and outdoor use, extending its life.
Machinability: Extruded aluminum tubes also have excellent machinability, and can be cut, bent, welded, etc. to achieve diverse shapes and sizes. This makes extruded aluminum tubes suitable for a variety of design needs, from simple components to complex structures, enabling precise machining.
Excellent electrical conductivity: Extruded aluminum tube, as a metal material, has good electrical conductivity, which means it can effectively conduct electric current. The electrical conductivity depends on the electrical conductivity of the material, and the extruded aluminum tube has a relatively high electrical conductivity, making it widely used in electrical and electronic fields, such as wires, cable jackets, etc.
High Strength: It is important to emphasize the strength characteristics of extruded aluminum tubing. Although extruded aluminum tubing is a lightweight metal, extruded aluminum tubing can achieve impressive strength through alloying. This makes it excellent in applications requiring load bearing and structural support.
Renewability: Renewability means that extruded aluminum tubing can be recycled over and over again without compromising its performance and quality. By recycling and reprocessing old aluminum products, we can achieve more efficient use and management of limited resources,
Various Surface Treatments: The various surface treatments of extruded aluminum tubes are designed to improve their appearance, performance and durability to suit different application requirements. These treatment methods can form different coatings, textures or protective layers on the surface of the extruded aluminum tube, thereby giving the extruded aluminum tube more functions and characteristics, such as anodizing, spraying, coating, etc., to increase its corrosion resistance, Aesthetics and functionality.
Environmental protection: The environmental protection and sustainability of extruded aluminum pipes is a factor that cannot be ignored. Aluminum profiles are recyclable materials, and their production and recycling processes have relatively little impact on the environment. This is crucial in today’s society, which is increasingly emphasizing sustainability.
Good surface quality: The high finish of the extruded aluminum tube can reflect light and look brighter and more refined. The surface quality of the extruded aluminum tube is high, easy to color, spray and carry out various surface treatments to meet the needs of different projects .
Types of Extruded Aluminum Tubes?
When we discuss the classification of extruded aluminum tubes, an important angle is to classify them according to their different shapes.
● square tube has a square cross-section. This makes the aluminum square tube very practical in some projects that require angles or even boundaries.
● Rectangular Tube is also a common type.Similar to square tubing, rectangular tubing is rectangular in cross-section, but it is usually taller or wider.Rectangular tubes are suitable for projects that require a larger area for load distribution,Such as for the manufacture of frames, door frames, furniture, etc. Its wide cross-section provides suitable support for larger loads.
● Round tubing is one of the most common types of extruded aluminum tubing.The cross-sectional shape of this extruded aluminum tube is circular and has very uniform distribution characteristics.Due to the advantages of a circular cross-section in terms of pressure and weight distribution, round tubes are widely used in many fields.From structural support to decorative design, round tubes can meet the needs of different projects.
● The elliptical tube has an elliptical cross-section. Oval tubes are often used for decorative and artistic designs.It can add a chic look and unique style to projects such as furniture, sculptures, vehicle exteriors and more.
● The working principle of the telescopic aluminum tube is based on its telescopic nature, its adjustability and lightness make it an ideal choice for many household and An important part of outdoor products. Whether in the home, outdoors, or commercial location, telescoping aluminum tubing offers convenience and flexibility.
What are the mechanical properties of aluminum profile doors and windows?
High strength. Aluminum is a metal material with high strength, and its hardness and compression resistance are relatively strong. During the manufacturing process of doors and windows, the fastness and bearing capacity of aluminum ensure the overall stability and safety of doors and windows.
Strong corrosion resistance. Aluminum has excellent corrosion resistance and can be used for a long time in various harsh environments without damage. This means that aluminum profile doors and windows will not corrode, rust, or deform, ensuring the long-term use of doors and windows.
Good thermal conductivity. Aluminum has good thermal conductivity, which can quickly transfer heat, reduce local heat accumulation in doors and windows, ensure indoor ventilation and uniform temperature distribution, and improve the comfort of doors and windows.
Lightweight. Aluminum is a lighter metal material that is easy to handle and install. Lightweight doors and windows play a very positive role in reducing the load of the overall building structure.
Different series of extruded aluminum tubes
When it comes to the selection of extruded aluminum tube material, it is very important to understand the difference between different types of aluminum alloys and heat treatment states.
Next let me explain you the difference between 6063 T5, 6061 T5 and 6061 T6 extruded aluminum tubing
First, let’s look at what each of these terms means:
6063, 6061: These are different types of aluminum alloys. Just as different ingredients can be used to make different dishes, different aluminum alloys can be used to make aluminum tubes with different properties.
T5, T6: These are the indications of the heat treatment state. Heat treatment is to change the properties of materials by controlling the heating and cooling process of materials. Both T5 and T6 are states of extruded aluminum tubes after different types of heat treatments.
So, what exactly is the difference between them?
6063 T5: This type of extruded aluminum tubing uses 6063 aluminum alloy and is heat treated T5. The T5 condition means that after extrusion, the extruded aluminum tube is artificially aged. In this state, the extruded aluminum tube has moderate strength while retaining good deformation properties. This makes it suitable for many architectural and decorative projects such as window and door frames and furniture.
6061 T5: In this case we use 6061 aluminum alloy, also heat treated T5. 6061 T5 extruded aluminum tubing has higher strength compared to 6063 T5. It is suitable for applications requiring higher strength, such as some industrial fields.
6061 T6: Finally, we have 6061 T6 extruded aluminum tubing, this time T6 heat treated. In the T6 temper, the strength of the extruded aluminum tube is further increased, but some deformation properties may be sacrificed. This makes it ideal for special applications requiring extremely high strength, such as some areas requiring compressive properties.
When selecting the right extruded aluminum tubing for your needs, it is critical to consider factors such as required strength, deformation properties, corrosion resistance and application environment. By understanding the characteristics of these different aluminum alloys and heat treatment states, you will be able to make more informed decisions to meet your project needs.
Production process of extruded aluminum tube?
1. Selection of raw materials: The production materials of aluminum tubes are mainly aluminum alloy materials and pure aluminum materials.Among them, the aluminum alloy material has the advantages of high strength and good corrosion resistance, and is suitable for production requirements.High-strength, high-corrosion-resistant extruded aluminum tube; while pure aluminum material has good thermal and electrical conductivityIt is suitable for extruded aluminum tubes that require high thermal conductivity and electrical conductivity.
2. Aluminum processing: Aluminum profiles need to be cut, polished, pressed and other processing procedures to make
Base material for extruded aluminum tubes.
3. Aluminum tube extrusion: Put the extruded aluminum tube base material in the aluminum tube extrusion machine for extrusion to deform it
Become a hollow extruded aluminum tube.
4. Aluminum tube welding: Extruded aluminum tubes need to be welded to ensure their strength and tightness. welding
Methods include gas welding, TIG welding and MIG welding, etc.
5. Surface treatment: through anodic oxidation, electrophoretic coating, spray painting and other surface treatment methods,
The extruded aluminum tube has the characteristics of corrosion resistance and beauty.
Manufacturing method of aluminum tube?
When talking about the manufacturing methods of aluminum tubing, there are four main methods: extrusion, cold drawing, hot drawing and welding.
1. Extrusion molding method:
Extrusion is a common manufacturing method used to produce aluminum tubes of various sizes.First of all, we need to prepare the aluminum billet and heat it to a suitable temperature so that it has enough plasticity. Then, the heated billet of aluminum is put into an extrusion press. Extruders apply pressure to extrude an aluminum billet through the bore of a die, forming the original shape of the aluminum tube.
2. Cold drawing method:
Next, let’s look at cold drawing, another method of aluminum tubing manufacturing. This method is suitable for aluminum tubes that require higher dimensional accuracy and better surface quality.
First, we need aluminum billets that have been heat treated or cold rolled. Then, through a series of cold drawing processes, the aluminum billet is gradually stretched and passed through dies with different diameters to finally form the aluminum tube size we need.
The cold drawing method can improve the mechanical properties of the aluminum tube, and at the same time ensure higher dimensional accuracy, which is very suitable for occasions with high quality requirements.
3. Hot drawing method:
We now turn to hot drawing, a method used to manufacture large diameter or specially shaped aluminum tubes.
In this process, the aluminum billet is first heated to a high temperature to increase its plasticity. Then, through the stretching process, the aluminum billet is stretched at high temperature, so as to realize the adjustment of size and the change of shape.
The hot drawing method makes full use of the enhanced plasticity of the material at high temperature, and can manufacture aluminum tubes of various complex shapes.
4. Welding forming method:
Finally, we come to weld forming, which is the method used to manufacture aluminum tubes with large diameters or where specific material combinations are required.
In the welded forming method, we use multiple aluminum sheets or strips and join them together through a welding process. Subsequently, through further processing and forming, the aluminum tubes we need are produced.
This method has high flexibility and is suitable for the manufacture of larger diameter aluminum tubes and products with special material requirements.
Connection method of extruded aluminum tubes?
Like building blocks when you want to connect two extruded aluminum tubes together
Solder Connections: First, let’s talk about soldering. Welding is the process of joining extruded aluminum tubes together by heating them and melting the metal at their contact points. This type of connection is very strong and is suitable for applications requiring high strength and tightness, such as piping systems and mechanical structures.
Threaded connection: Another common connection method is the threaded connection. You can imagine, like a nut and bolt, an extruded aluminum tube with a thread on the end and a second tube with a matching thread that is twisted to connect them together. This method is suitable for situations that require frequent disassembly and assembly.
Socket connection: The third method is socket connection, similar to the sockets of toy blocks. One end of one extruded aluminum tube is inserted into the end of another extruded aluminum tube, usually with a sealing material to ensure that the connection is watertight. This approach is suitable for some smaller applications, such as home improvement.
Mechanical Connection: The mechanical connection tightly connects two extruded aluminum tubes together by using special mechanical devices such as snap rings, clips, etc. This method is usually suitable for situations that require quick installation and disassembly, such as temporary structures.
Quick Connect: Lastly, we have the Quick Connect. These fittings use snaps or other mechanisms that allow two extruded aluminum tubes to be easily connected and disconnected. This is convenient in applications that require frequent replacement or maintenance.
Quality testing of extruded aluminum tubes?
When we talk about the quality testing of extruded aluminum tubes, we need a clear goal to ensure that the extruded aluminum tubes meet specific standards and requirements to guarantee their safety and reliability in various applications. The quality testing of aluminum tubes involves many aspects, let us understand these key testing contents step by step.
Chemical Composition Analysis
This step is to determine the content of various elements in the extruded aluminum tube, which are critical to its performance. Through spectral analysis, mass spectrometry and other methods, we can accurately know the content of various metal and non-metal elements in the extruded aluminum tube to ensure that they meet the predetermined ratio and standard.
Physical property test
These tests deal with aspects such as strength, hardness, impact capability and fatigue durability of extruded aluminum tubes. We use tensile tests to understand the tensile strength and yield strength of extruded aluminum tubes under tension. Hardness testing helps us understand the surface hardness of extruded aluminum tubes, which is critical for use in various working environments. Impact testing tells us how an extruded aluminum tube will perform in a crash, while fatigue testing looks at its durability under long-term alternating loads.
Dimensional and geometric performance testing
These tests ensure that the size and shape of the extruded aluminum tubing conforms to the specified requirements. We measure dimensional parameters such as outside diameter, wall thickness and inside diameter, as well as geometric properties such as straightness and roundness, to ensure that extruded aluminum tubes will fit and perform correctly when assembled and used.
Surface quality test
We inspect the surface for defects such as cracks, air bubbles, inclusions, etc., to ensure that the appearance and quality of the extruded aluminum tubes are as expected. Coating adhesion and uniformity are also assessed in this test to ensure that the coating is not flaking or uneven.
Corrosion and Weatherability Testing
These tests simulate conditions under different environmental conditions to examine the corrosion and weather resistance of extruded aluminum tubing. This is especially important for outdoor and wet applications, ensuring that extruded aluminum tubing will maintain its performance and appearance in all conditions.
non-destructive testing
Through techniques such as ultrasonic testing, X-ray inspection and magnetic particle inspection, we can find defects inside the extruded aluminum tube without destroying the integrity of the extruded aluminum tube. This helps to ensure that the internal quality of the extruded aluminum tube meets the requirements.
Specifications and standards for extruded aluminum tubes?
1. Diameter specifications
The diameter specification of the extruded aluminum tube refers to the cross-sectional diameter of the tube,Common diameter specifications of extruded aluminum tubes are 6mm, 8mm, 10mm, 12mm, 15mm, 20mm, 25mm, 30mm, etc.
Diameter is usually expressed in mm.
Extruded aluminum tubes of different specifications are suitable for different scenarios,
For example, those with smaller diameters can be used to make small parts such as power coils and sprayers,
The larger diameter can be used to build large structures such as tent brackets and display racks.
2. Wall thickness specifications
The wall thickness specification refers to the thickness of the extruded aluminum tube wall, usually expressed in mm.
The wall thickness specification of the extruded aluminum tube directly affects the strength and stability of the extruded aluminum tube, and also affects the service life of the extruded aluminum tube.
Generally speaking, smaller diameter specifications will be equipped with thinner wall thicknesses, while larger diameter specifications will be equipped with thicker wall thicknesses.
3. Length specification
The length specification of the extruded aluminum tube refers to its length, which is generally expressed in mm.
Common length specifications are 1000mm, 2000mm, 3000mm, etc. The selection of length specifications needs to be determined according to specific needs.
Straightening method of extruded aluminum tube?
When it is necessary to restore a bent or deformed extruded aluminum tube to its original shape, we can use different methods to straighten it. Below, I will explain to you some common straightening methods for extruded aluminum tubes:
1. Mechanical alignment:
Mechanical alignment is a common and effective method. It involves placing extruded aluminum tubes in specially designed machinery equipped with a series of rolling units. By being gradually rolled through these rollers, the extruded aluminum tube is subjected to progressively less force, returning it to its original shape. The process is similar to how we roll dough in a bread machine, but of course with more precision.
2. Hydraulic alignment:
Hydraulic straightening is another common method for pipe with larger diameters or thicker walls. In this method, we’ll place an extruded aluminum tube in a fixture, and then apply just the right amount of hydraulic pressure. This force will gradually straighten the tube, just as we flatten a piece of paper with a wheelbarrow.
3. Thermal alignment:
The thermal straightening method involves heating the extruded aluminum tube to a specific temperature. By heating, the extruded aluminum tube becomes more flexible and pliable. Once the proper temperature is reached, we can use mechanical means, such as rolling or stretching, to straighten the tube. As the tube cools, it will retain its straightened shape.
4. Rolling straightening:
Roll straightening is similar to mechanical straightening, but in this case, extruded aluminum tubes are fed into a rolling mill where they are rolled over rollers to gradually straighten. This can be cold rolling or hot rolling, depending on the characteristics of the tube that needs to be straightened.
5. Stretch straightening:
In the stretch straightening method, we fix an extruded aluminum tube between two fixed points and apply a stretching force. This process gradually returns the tube from its bent state to a closer to its original shape.
6. Electric heating alignment:
The electric heat straightening method works by applying electric heat to the extruded aluminum tube to soften it. We can then use mechanical means, such as rolling, to straighten the tube.
Regardless of the method used, the parameters need to be carefully controlled to ensure that the straightening process does not cause the tube to crack or deform excessively. It is best to carry out these alignment methods under the guidance of professionals to ensure safety and effectiveness.
Anti-corrosion treatment of extruded aluminum tube?
When it comes to protecting extruded aluminum tubes from corrosion and damage, prolonging their service life, the anti-corrosion treatment of extruded aluminum tubes becomes crucial. Let’s discuss some common anti-corrosion treatment methods for extruded aluminum tubes:
Anodizing:
Anodizing is a classic surface treatment for extruded aluminum tubing. In this process, extruded aluminum tubes are placed in an acidic electrolyte and an electric current is applied. This results in the formation of a dense oxide layer on the surface of the extruded aluminum tube, known as the oxide film. This layer of oxide film not only increases the corrosion resistance of the extruded aluminum tube, but also adds color to it to create various decorative effects.
coating:
Coating is another common method in which the surface of the extruded aluminum tube is covered with a layer of anti-corrosion paint, lacquer or film. The coating forms a barrier between the outside environment and the aluminum, protecting extruded aluminum tubes from corrosion.
Epoxy coating:
Epoxy coatings are widely used where high corrosion resistance is required. This coating provides effective protection against chemical attack and also has excellent wear resistance. It acts like a solid layer of armor, providing extra protection to the extruded aluminum tubes.
plating:
Electroplating is the method of depositing another layer of metal onto the surface of extruded aluminum tubing. Through electrochemical reaction, a layer of metal coating, such as nickel, chromium, etc., is formed on the extruded aluminum tube. This not only improves the corrosion resistance of the extruded aluminum tube, but also gives it more decorative effects.
Organic coating:
Organic coatings, such as polymer coatings, can form a protective film on the surface of extruded aluminum tubing. This film can effectively isolate the external environment and prevent corrosion and oxidation.
Hot-dip galvanizing:
Hot-dip galvanizing is a method in which extruded aluminum pipes are immersed in molten zinc to form a zinc layer on the surface. This zinc layer provides additional corrosion protection to the extruded aluminum tube, making it better resistant to corrosion in harsh environments.
Alloy selection:
In the manufacturing process of extruded aluminum tubes, the selection of alloys with good corrosion resistance is also an important anti-corrosion strategy. These alloys can have their own corrosion resistance to some extent, which provides more protection for the use of extruded aluminum tubes.
Application of extruded aluminum tube?
When talking about the applications of extruded aluminum tubing, we can’t help but think of the various uses of this lightweight, corrosion-resistant material in our daily lives and in industries. This material plays an important role in a variety of industries. Let’s take a look at how extruded aluminum tubes work in different fields.
Construction and building materials:
First, let’s start with the field of architecture. Have you ever noticed that many modern buildings use extruded aluminum tubes for their structures, windows, doors and stair rails? The lightness of extruded aluminum tubing makes it ideal for constructing large buildings and homes. At the same time, its corrosion resistance also ensures the long life of the building.
Transportation:
In the field of transportation, the application of extruded aluminum pipe is also significant. Whether it’s a car, train or airplane, extruded aluminum tubes are used to create body structures and components. Thanks to the lightweight nature of the extruded aluminum tubes, the overall weight of the vehicle is reduced, resulting in improved fuel efficiency and reduced energy consumption.
electronic product:
Stepping into the field of electronics, extruded aluminum tubes play an important role in the manufacture of electronic devices. The casings of your computer, cell phone, and other electronic devices most likely contain extruded aluminum tubing. Due to the good thermal conductivity of the extruded aluminum tube, it helps to stabilize the temperature of the device and prevent overheating.
Energy industry:
In the energy industry, extruded aluminum tubes are used to make components such as solar water heaters and wind turbine wings. Its light weight makes these energy devices more efficient, while the corrosion resistance of the extruded aluminum tube also ensures the stable operation of the equipment in harsh environments.
Industrial equipment:
In the field of industrial equipment, extruded aluminum tubes are widely used in pipelines for transporting fluids such as liquids and gases. Its lightness makes installation and maintenance easier and helps reduce costs.
In conclusion, extruded aluminum tube, as a versatile material, plays an indispensable role in our life. Whether in construction, transportation, electronics, energy or industry, extrusion
Extruded aluminum tubes all stand out with their unique advantages. Its lightness facilitates a variety of applications, its corrosion resistance ensures a long service life, and its excellent thermal conductivity makes it useful for temperature control.