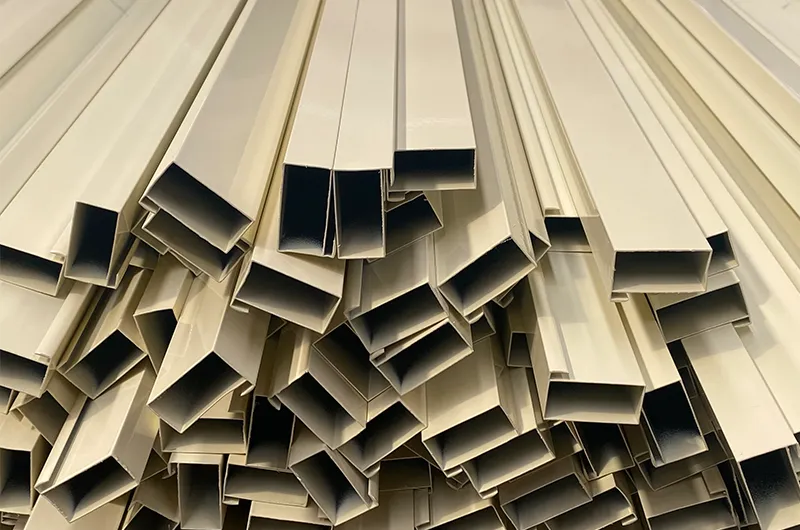
Powder coated extruded aluminum profiles
- Received national honors
- Quality is our first concern
- 31 years of production experience
- Production equipment is imported from abroad
Your Preferred Powder Coated Extruded Aluminum Profile Manufacturer
Powder Coating is a coating process that uses solid powder coating to adhere to the surface of the workpiece through electrostatic attraction, and then melts, flows and solidifies under high temperature conditions into a hard coating.
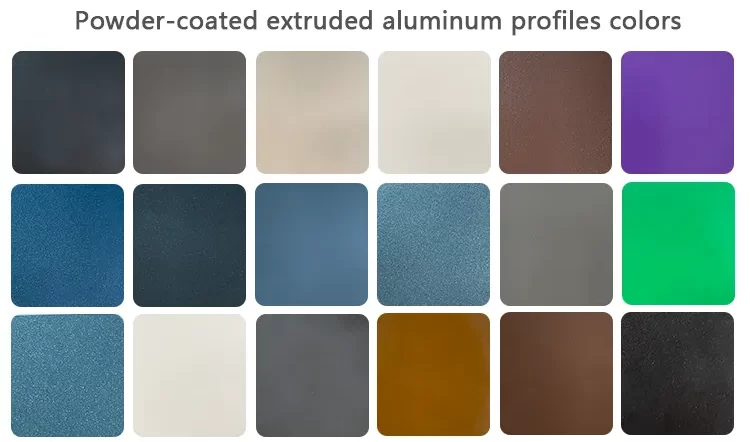
Before powder coating, Xingda performs surface treatment on extruded aluminum profiles, including cleaning, degreasing, and possibly acid etching or shot blasting to ensure proper adhesion of the coating.
Xingda uses professional powder coating equipment to evenly apply powder coating on the surface of extruded aluminum profiles through the principle of electrostatic attraction.
Xingda Aluminum will conduct a series of quality controls during the spraying process, such as adhesion testing, coating thickness testing, appearance inspection, etc., to ensure that the quality of the coating meets the requirements.
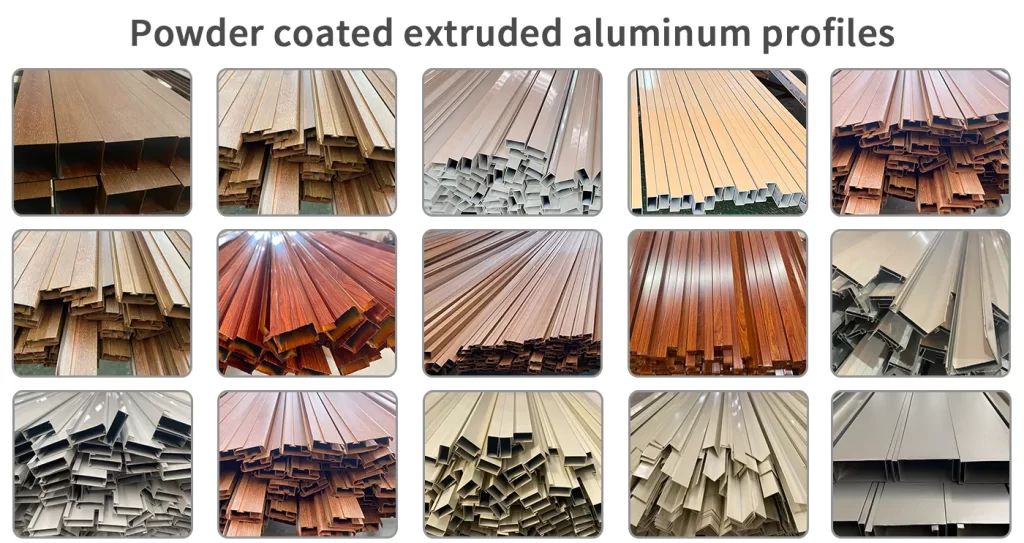
Powder-coated extruded aluminum profiles typically offer excellent corrosion resistance, wear resistance and aesthetics, effectively protecting the aluminum profile.
Xingda powder-coated extruded aluminum profiles remain stable in high temperature environments and are suitable for some applications that require high temperature resistance.
Xingda powder-coated extruded aluminum profiles are widely used in construction, furniture, automobiles, electronic equipment and other fields to improve the surface protection performance and aesthetics of products.
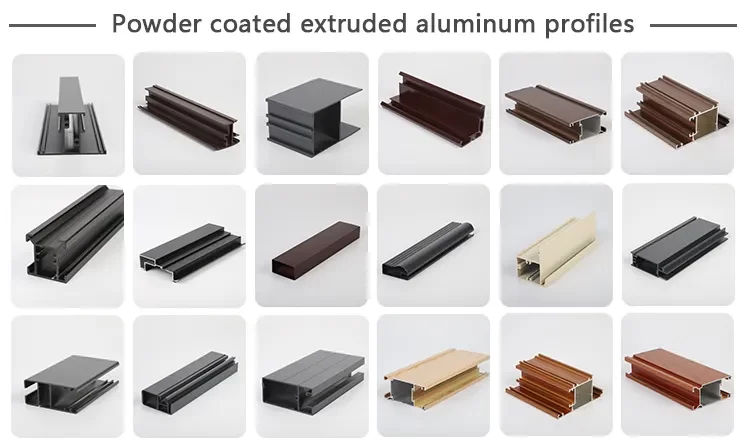
The process flow of powder coated extruded aluminum profiles
When the Xingda factory adopts the powder coating extruded aluminum profile process, it usually goes through the following stages:
1. Order receipt and material preparation:
• First, the factory will receive the customer’s order, which includes the specifications, quantity, color and other requirements of the extruded aluminum profiles to be powder coated.
• After receiving an order, the factory prepares the required extruded aluminum profiles along with the corresponding powder coating.
2. Preparation of extruded aluminum profiles:
• Extruded aluminum profiles may undergo some pre-processing on the production line such as cutting, trimming and straightening to ensure compliance with specifications.
3. Surface treatment:
• The surface of extruded aluminum profiles may undergo a series of treatment steps, such as cleaning, degreasing, shot blasting or pickling to ensure the surface is clean and smooth to facilitate coating adhesion.
4. Powder coating:
• Using special electrostatic spraying equipment, workers will spray powder coating evenly on the surface of the extruded aluminum profile.
• During the spraying process, attention needs to be paid to controlling the spraying distance, spraying speed and powder uniformity to ensure the quality of the coating.
5. Baking and curing:
• After spraying, the extruded aluminum profiles are fed into an oven or hot air furnace to cure the coating at high temperatures.
• Temperature and time will be determined based on the type and thickness of powder coating used.
6. Cooling and quality inspection:
• After curing is complete, the extruded aluminum profile is removed and allowed to cool to ensure the coating is fully cured.
• Conduct a visual inspection of the coating to check for defects such as bubbles, sags, holes, etc.
7. Quality control:
• Conduct a series of quality tests, including adhesion tests, corrosion resistance tests, etc., to ensure that the performance of the coating meets the requirements.
8. Packaging and labeling:
• After completion of quality inspection, the coated extruded aluminum profiles are packaged to protect the coating from the external environment.
• During the packaging process, corresponding identification may be attached, including model, color, production date and other information.
9. Storage and Logistics:
• After packaging, the powder-coated extruded aluminum profiles are stored in a dry and ventilated warehouse away from moisture and chemical contact.
• Arrange appropriate logistics means to transport finished products to the location designated by the customer.
10. Recording and reporting:
• The factory will retain relevant records during the production process, including order information, production records, quality inspection reports, etc., for future reference.
Each link in the above process requires strict operation and quality control to ensure that the final product meets customer requirements and industry standards. At the same time, the factory may make some customized process adjustments based on actual conditions to meet the needs of specific projects.